FAQs
Transcripts from the Q&A Sessions will be added here
along with answers to questions received via email.
Additional materials as mentioned in the Q&A #2 Session (updated 1/6/2023)
- Drawings of the gondola – We went with a few images (easier) to show the mounting posts (blue) with respect to the rest of the gondola. Note the blue posts have the 100mm ¼-20 spacing as called out in the requirements. A supplementary drawing of the L-channel (blue rails shown in the gondola drawings) is also provided.
- Historic flight data – see three flight data files from CSBF (similar to what we expect for this challenge). Note this data is RAW, in that there are errors caused by false sensor readings, telemetry errors, etc. Teams are encouraged to “scrub” this data before use.
- Data vault drawings – coming soon.
- Power – pigtails of 28 VDC signal will be provided. If there is a connector change closer to flight, the teams will be given either the connector itself or the part number to procure it.
- List of batteries – Any battery with a UL certificate is allowed. See example data sheet and UL certificate.
Emailed Questions (updated 1/5/23)
Q1: Our team was in disagreement with our interpretation of the challenge guidelines on prohibited items. Some read “Chutes and drag systems unallowable by FAA limits” to mean that parachutes are allowed within FAA guidelines while others read it as not being allowed at all. This is especially confusing for us because the background and context of challenge guidelines invite us to learn from a successful project that used a parachute to retrieve data during flights in Canada.
A1: Parachutes and drag systems are allowed as long as they meet FAA requirements.
Q2: The language is a little unclear about the mounting of the deployment subsystem. It says mounted vertically, does this mean that the L channel is horizontal and the system mounts to the bottom of it, or is the L channel vertical and the system mounts to the side of it?
A2: The L-channel runs vertically and the deployer mounts vertically as well.
Q3: I have a quick question regarding the NASA FLOATing DRAGON competition. The HASP student interface description on the main website provides documentation on the interface afforded to payloads, but we didn’t see specific mention of the signal that will be sent to the student node vehicle for deployment. Is the signal coming from the gondolas an analog signal or will we receive notification to deploy digitally/serially via the RS-232? If this is a raw analog signal, is it coming from the same interface that provides the RS-232 connection?
A3: The HASP gondola interface is not how the interface is connected for this flight. Instead, the gondola will have a similar physical shape/design as those used for the HASP gondolas. The electrical interface between the deployer and CSBF will be a pigtail (two wires) to receive the signal to drop. No power will be provided the signal should be an analog signal.
Q4: I had a question about the deployer for the challenge. We had interpreted it as the deployer shall drop the node and the node would autonomously land to the landing zone. With this, we planned the design around all hardware being present mainly in the node system itself. However, when reviewing the first Q&A, as none of my team was present for that one, I saw that it was mentioned that the deployer itself would be the one holding the flight computer and all electrical components. I was just hoping for some clarification on that if possible.
A4: The deployer should hold all items required to maintain the node in a ready state prior to drop, for example battery power to keep the node powered during rollout, launch, and ascent. The flight computer is somewhat ambiguous, since that could refer to the computer to select the waypoints, or the computer to actuate/guide the node to the ground. The general idea is that anything that needs to fly to maintain the node can be kept in the deployer, but items required to ensure successful navigation during descent should be packaged in the node.
Q5: I have a question regarding the general comments released after the PDR submissions. It is stated that “It will not be possible to communicate with your payload during the flight, it must be autonomous.” Are we allowed to downlink data from our flight that way we can follow it in real-time, in addition to logging this data and examining after payload recovery? Or is this considered communication and is not allowed.
A5: Student provided systems that can downlink telemetry will likely be allowed to. NASA is working with the FAA on how to classify these systems and what flight rules will be required / enforced.
Q6: How far apart are the mounting posts are on the gondola?
A6: Greater than 45 cm.
Q7: One of the bullet points on the guidelines document tells us that we should “Provide details of the integration plan.” Does it refer to how our node will connect to the gondola, and how our project will be integrated into the larger structure?
A7: The student teams need to write down what they are going to do upon arrival at Fort Sumner. It should be fairly detailed. For example:
- Attach deployer to gondola
- Interface with electrical connections provided by CSBF
- Test electrical commanding signals
- Etc.
- Prep node for installation
- Install batteries into system
- Install NASA provided payload.
- Etc.
Q8: Is there a CAD model available for the gondola drawings provided in the FAQ resource?
A8: See link above for drawings showing the general layout of the gondola and the mounting point (of the L-channel). We won’t be providing the gondola CAD since it is a generic gondola and will change based on the other missions flying with us.
Q9: Can we modify our team members list? If yes, how do we do so?
A9: Yes, as long as they stay in the requirements provided.
Q10: What happens in the case where multiple teams want to deploy at the same time? How are the teams prioritized?
A10: All teams will be flying from the same gondola. If two teams want to deploy at the same time, then one team will deploy ~15 seconds early and one will deploy ~15 seconds late, providing about a 30-second gap between deployments. This should allow enough time for the two nodes to avoid each other while providing approximately the same drop location.
Q11: It was mentioned that the maximum distance that our node would have to travel is 45km from the deployment point. Is this specification still valid?
A11: Yes.
Q12: What will be required of the physical point of communication to verify operation of the deployment system post-test?
A12: The deployment system will be verified by observation of the release of the node from the deployer. This will be done via video during flight. Thus there should be no verification of operations for the point of communication post-test.
Q13: What will be considered “verified operation”?
A13: I’m not sure what document you’re referring to here. Can you please point to a reference so I can give better guidance?
Q14: Will there need to be some automatic data transfer?
A14: No. NASA will receive the data from our data vaults post-flight.
Q15: Additionally, what are the details of the “signal” sent to trigger payload drop? I have seen elsewhere that a 28VDC signal will be provided over a pigtail connector– 28V seems a bit excessive for control of an analog switch or some other mechanism, which is what I had in mind.
A15: The release signal will be a 28 VDC signal. Expect it to be a “pull high” type of signal (i.e. low/no power, just a voltage reference).
Q16: The physical point of communication is on the deployment subsystem, but is meant to access a microcontroller on the node subsystem. Does this mean that we will have to run a cable from the node subsystem to the deployment subsystem which will then have to be disconnected on drop?
A16: No, the communication between the gondola and the deployer is all that is required. There is no requirement to interface with the microcontroller/flight computer on the node at all. That is a choice left to the teams.
Q17: Our team was hoping for CAD drawing of the actual mounting system. The CAD images supplied looks like a box that holds it, but nothing to actually mount onto. Is this the entire mounting system that we will be using or is there more to it?
A17: Drawings and detailed images coming soon. The mounting datum is three (3) ¼-20 holes spaced 100mm apart on Aluminum L-channel. The deployer must mount to the L-channel.
Q18: I noticed that in the challenge guidelines on the third page, the second sentence in the first paragraph under the nomenclature section states that the competition coordinators will supply a signal that will drop the project from the balloon. As in we will choose when to drop and then [NASA] will press a button to actually drop. But in the feedback, we received, it made is seem like we had to create a deployment mechanism.
A18: We will provide an electrical signal but not a mechanical system that will actually release the node.
Questions Regarding the Raw Data for Historical Flights
Q: What does “MBS”, “DRAD” mean?
A: “MBS” is millibars (pressure reading), “DRAD” is downward radiation (measurement using degC, not important).
Q: For the 3 flights, was the descent controlled or free fall?
A: Free fall.
Q: What are the units for the columns?
A: The units should be as follows:
TIME: Zulu time, HH:MM:SS
BAR ALT: Barometric pressure converted to altitude, kft
MBS: Barometric pressure, millibars
AIRT: Air temperature, degC
DRAD: Downward radiation temperature measurement, degC
LAT: Latitude, degrees – minutes
LON: Longitude, degrees – minutes
GPS ALT: Altitude from GPS, meters
Q: Moreover, what is the maximum wind speed that our system should be able to handle?
A: This is somewhat of a trick question, since the system doesn’t really care about the atmospheric wind sped per say. Your system should care about the relative wind speed, which will be a function of your system design and the descent velocities (and to a certain extent, your horizontal velocities). Thus it is more up to your team to model the designed system to understand what relative wind speed will be seen.
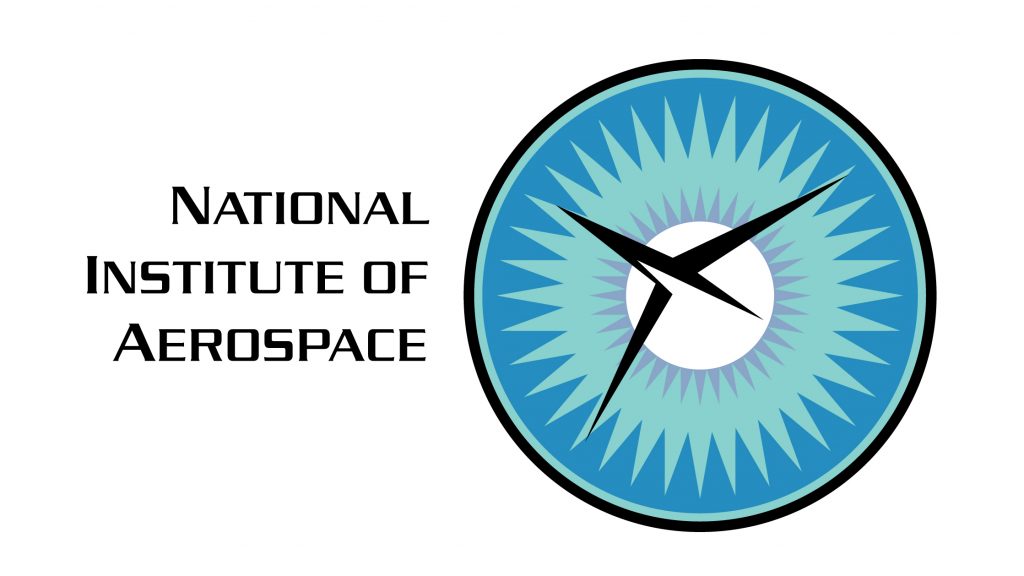
FLOATing DRAGON is managed by the National Institute of Aerospace on behalf of NASA’s Wallops Flight Facility’s Balloon Program Office.